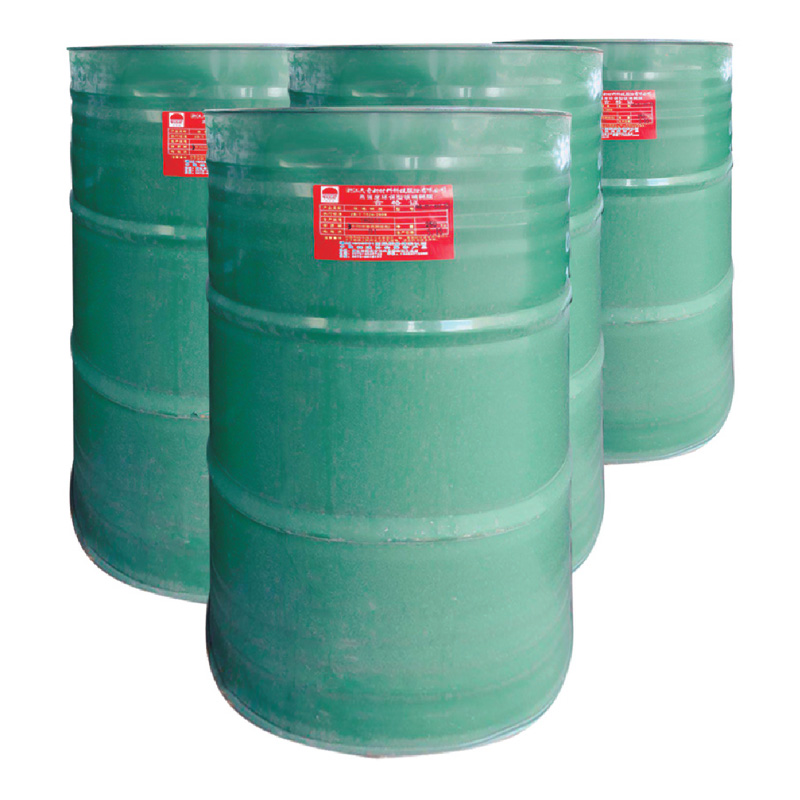
Phenolic Resins:
Alkaline phenolic resin is a subtype of phenolic resin, characterized by its alkaline pH during the curing process. Traditional phenolic resins typically have an acidic pH.
Alkaline phenolic resin offers enhanced adhesion to substrates and improved resistance to water, chemicals, and high temperatures compared to acidic phenolic resins.
It is commonly used in applications requiring high-temperature resistance, such as foundry cores and molds, abrasive grinding wheels, and friction materials.
Epoxy Resins:
Epoxy resins offer excellent mechanical properties, chemical resistance, and adhesion to various substrates.
Compared to epoxy resins, alkaline phenolic resin may have superior heat resistance and dimensional stability, making it suitable for applications exposed to elevated temperatures.
Epoxy resins are commonly used in structural adhesives, coatings, composites, and electronic encapsulation due to their versatility and high-performance properties.
Polyester Resins:
Polyester resins are known for their low cost, ease of handling, and good mechanical properties.
Alkaline phenolic resin typically exhibits better heat resistance, chemical resistance, and dimensional stability compared to polyester resins.
Polyester resins are commonly used in fiberglass composites, laminates, casting, and surface coatings for applications requiring moderate performance at a competitive price point.
Polyurethane Resins:
Polyurethane resins offer excellent flexibility, impact resistance, and abrasion resistance.
Alkaline phenolic resin may have superior heat resistance and dimensional stability compared to polyurethane resins, especially at high temperatures.
Polyurethane resins are commonly used in elastomers, coatings, adhesives, foams, and sealants for applications requiring flexibility, resilience, and durability.
Acrylic Resins:
Acrylic resins offer good weather resistance, clarity, and color retention.
Alkaline phenolic resin may provide better chemical resistance and heat resistance compared to acrylic resins.
Acrylic resins are commonly used in architectural coatings, automotive finishes, adhesives, and dental materials due to their aesthetic appeal and weatherability.
Alkaline phenolic resin exhibits specific performance advantages, such as enhanced heat resistance, adhesion, and chemical resistance, compared to other types of resins. Its suitability for different applications depends on factors such as temperature requirements, chemical exposure, mechanical properties, and cost considerations. By understanding the unique properties and performance characteristics of alkaline phenolic resin, manufacturers and engineers can select the most appropriate resin type for their specific application needs.